Summary
One tonne an-hour medical waste incinerator installed in Kuwait for MRC to improve environmental sustainability.
- C1000 Clinical Incineration Facility
- Automated Loading Systems
- Optimised Contaminated Waste disposal
- Waste-To-Energy Facility
- Dispose Of Hospital and Health Centre Waste
- Hot Water Heating Generation
Transforming Medical Waste Disposal In Kuwait
Following over two years of development, we were incredibly proud to formally hand over the controls to the final high-capacity installation of 2022. Completing the project on behalf of MRC Kuwait's leading recycling and eco-industrial company, well known for innovating in the field of waste management in Kuwait.
This project, funded in conjunction with the Ministry of Health, has a processing capacity of 24 tonnes per day and is designed to safely dispose of clinical, medical, and liquid waste through incineration. The Addfield C1000, which will be a part of MRC's network of disposal centres, is expected to operate 24 hours a day, 330 days a year (for a total of approximately 8,000 hours per year), serving hospitals and health centres throughout Kuwait.
The construction and installation of this facility took place during one of the most challenging times in recent memory due to the impact of the coronavirus pandemic, making this accomplishment all the more significant.
Combatting The Rise In Hazardous Waste In The Middle East
Our design engineers thoroughly reviewed all of the technical requirements due to the composition of the planned waste for this facility before beginning the final development phase. Overall more than 2000 design hours were invested from start to finish to ensure that the installation could sustainably manage all of the expected workflows and waste types that it will experience daily.
As a result of all discussions and requirements, it was agreed that a C1000 stepped heart incinerator with advanced filtration systems was the most suitable model to work from. The facility now stands well over three stories in height and was completed with additional clinical waste management systems, including an integrated weighbridge, automated bin lifter and tippler able to lift 1000+ litre waste bins for safe loading into the ram charger before entry into the primary stepped hearth chamber.
An automatically adaptive sequential waste charging system was included to ensure consistent waste throughput. As each sequential load of waste is pushed into the primary chamber via the ram charger, the previous loads are moved to the next incineration stage, agitating the waste and increasing the oxidation of any hazardous waste. It becomes finer at each step before finally being reduced to less than 5% of its original volume and removed from the chamber through the automatic conveyor for safe final disposal of ash.
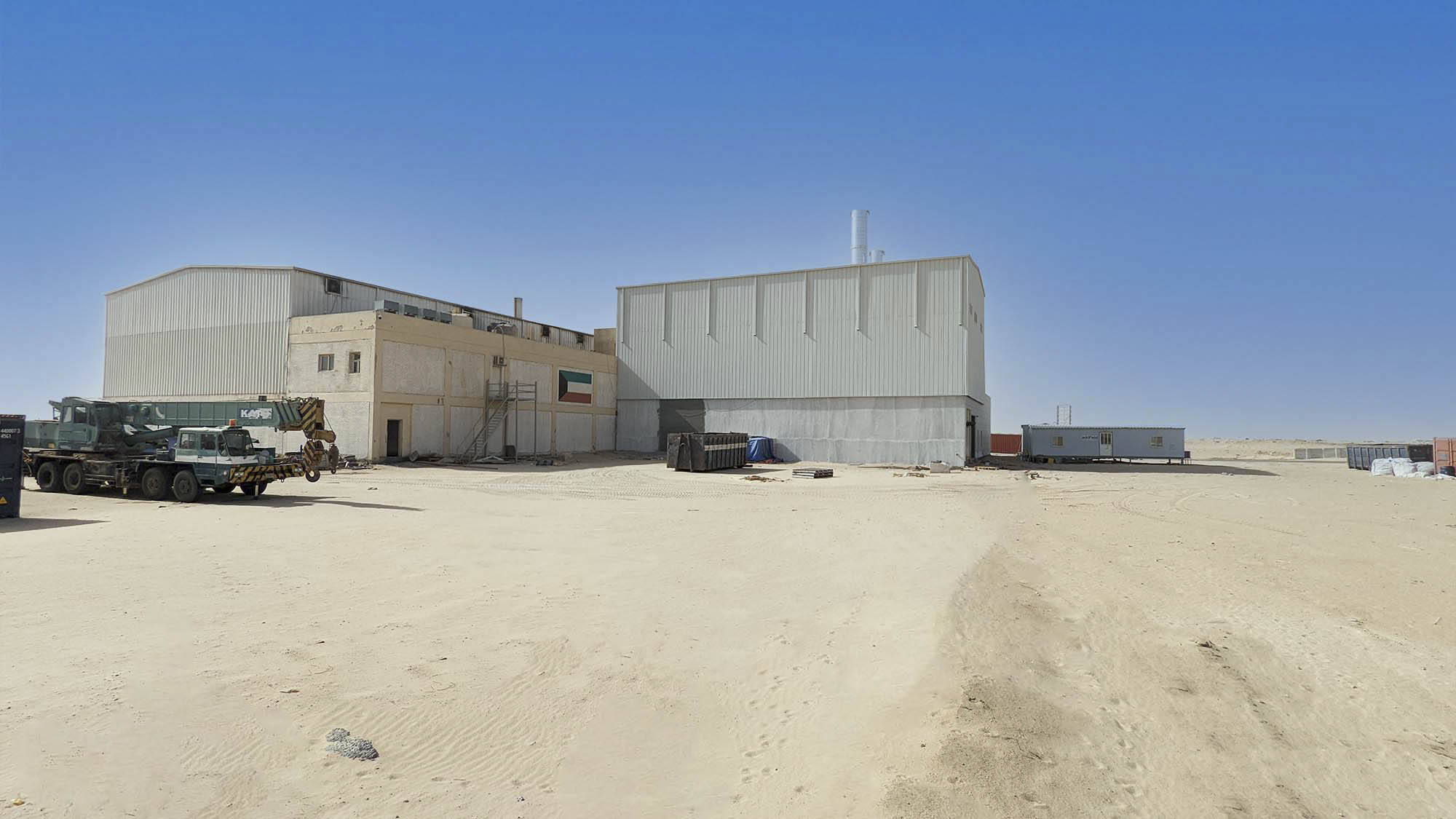
Custom Solution For Demanding Requirements
Due to the high levels of potentially toxic medical waste going through the C1000, it has been developed to operate under what is known as 'Starved Air Conditions'. This system redirects the gasses released by the waste directly into the secondary after chamber, where they are further subjected to a turbulent flow of ultra-heated air to achieve the complete oxidation of all flue gasses created during the incineration process.
The mammoth ten-tonne secondary chamber of the C1000 continues the process. Rather than destroying the waste, its purpose is to clean the gasses before releasing them into the environment.
A two-second retention time is required to ensure legislation is adhered to. Once the flue gasses have passed through the chamber, they enter the energy recovery phase. The high-temperature gas travels through a boiler system to create clean hot water for use across the entire facility and adjacent buildings. The last stage of the journey takes the gasses through a final filtration system combining sodium bicarbonate, activated carbon powder and a urea solution. These chemicals are forcibly injected into the gas stream before it enters the ceramic filter towers, which collect any remaining air pollutants.
The exhaust system includes a variable speed-induced draught fan, drawing gasses through the process. The C1000 is equipped with an accredited and WID/IED-compliant continuous emission monitoring system linked to the control-room-based SCADA system. Providing a permanent and continuous recording of all flue gas emissions, crucial when disposing of one tonne of medical waste every hour.
Constructed Through Challenging Times
Construction on the project began in February 2020, just as the coronavirus pandemic emerged. Despite the challenges posed by lockdowns and resource management difficulties, the construction progressed over the following 18 months. Completing a full 'Factory Acceptance Test' as the final stage in production in November 2021. This test ensures that every machine element functions as expected before it is shipped out. After passing all tests, the C1000 was shipped to Kuwait over several days using heavy-load capable wagons.
In February 2022, our team of engineers travelled to Kuwait to begin a six-month installation process due to the size and complexity of the facility. Our team worked alongside local engineers and operatives to put the facility into operation, with an expected operational life of over 20 years. Addfield also provided a comprehensive operation and maintenance training program for local engineers during the final installation and commissioning stage.
This Project Has Included:
Persistent Support Throughout
- Turn-key supply
- Design – engineering – manufacturing – installation – commissioning – training – proving – handover
- Compliant to the Waste Incineration Directive EC 2000/76 and Industrial Emission Directors IED 2010/75/EU
- Automatic loading bin tipper system
- Automatic de-ashing
- Energy recovery system
- De-Nox kit installed
- Sorbent reagents used for further neutralisation
- Dry ceramic filter system
- Full MCERT’s accredited 24/7 online continuous emission monitoring
MRC chose to work with Addfield after carefully reviewing other manufacturers from England, France, Germany, and the United States. The decision was based partly on our reputation for consistently delivering high-quality solutions for extensive incineration facilities internationally.
During the latter stages of construction, we were honoured to welcome a full delegation from Kuwait to our facility in the UK, consisting of senior business people and ministers. The delegation travelled nearly 3,000 miles to conduct their due diligence, meet the team behind the project, and explore future opportunities.
It is valuable for our customers to witness the skill and craftsmanship that goes into every element of the machine during its assembly. Often a highlight for visitors to the factory, as they can see where their new machine is being built and meet the people who are constructing it.
This project has been a great success for us at Addfield, and it is a testament to the quality of our work and the confidence Made in Great Britain carries around the world. The recognition we have received is also a clear investment in the quality and reliability of British manufacturing, as celebrated by the Department for International Trade's 'Exporting is Great' initiative."